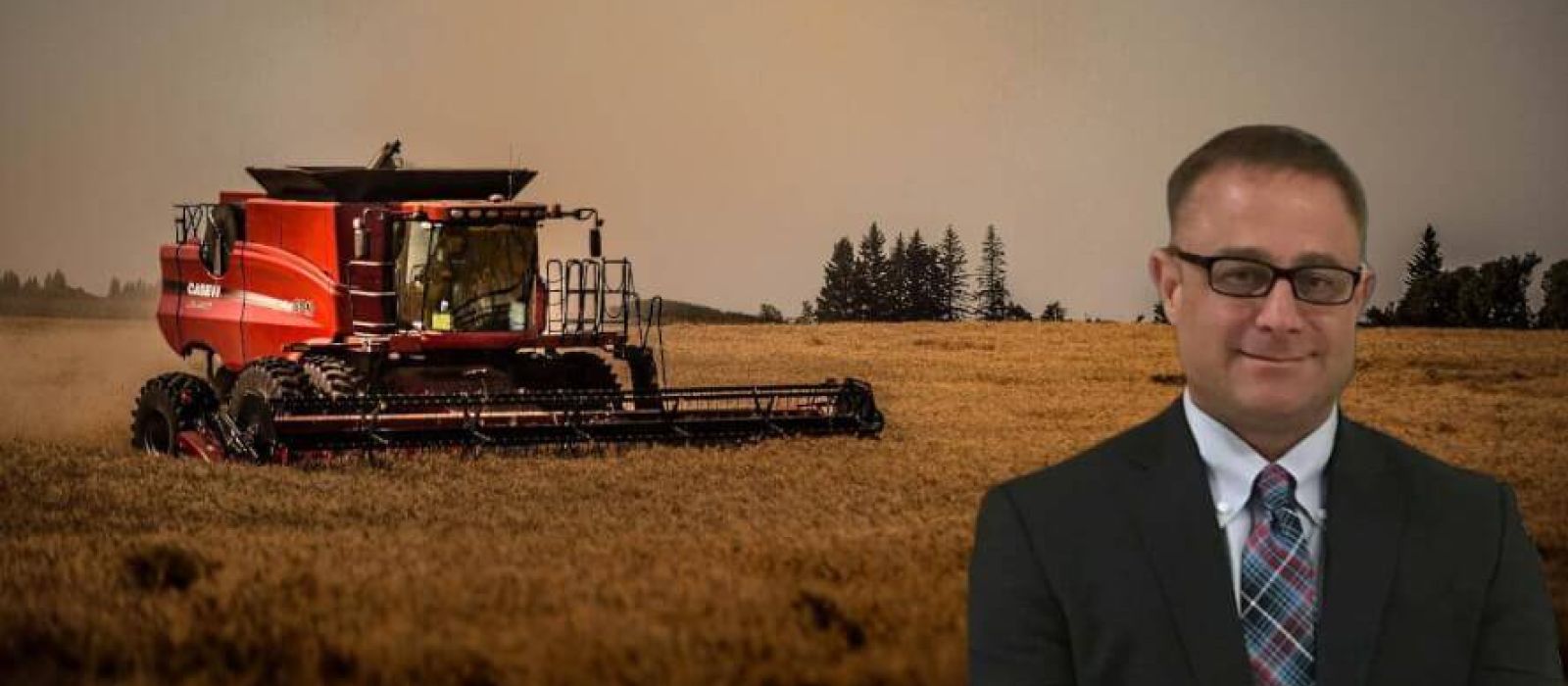
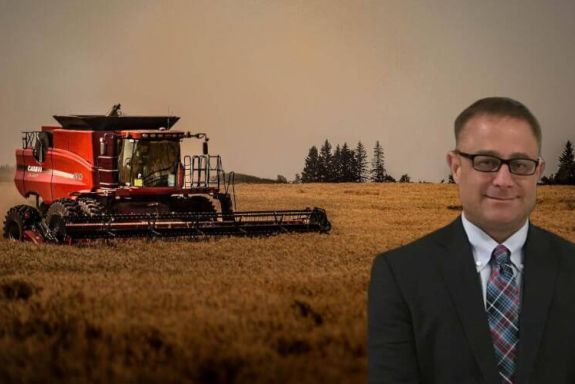
If we don’t win, you don’t pay.
NO WIN – NO FEE

ON CALL 24/7

U.S. Marine

Welcome to the Ehline Law Firm Personal Injury Attorneys, APLC page discussing harvester machines, farm labor vehicles, accidents, injuries, the law, and compensation. I am attorney Michael Ehline. I am one of the few highly experienced harvester, chipping, and shredding machine accident attorneys in the Golden State. I am an expert in the function and safety protocols required for constructing and using these farming contraptions.
And with the help of my trusted staff, I have built up a proven track record of litigating and resolving these curious and tragic events.
Below, I will discuss some history of California farming, harvesting, and injuries inherent in the agricultural industry related to laborers and machine cropping.
Also, below, I cover the biomechanics, causes, and prevention of mechanical and non-mechanical harvesting-related injuries. We won’t cover wage and hour, employment law, or discrimination disputes here.
But you can check out the employment law section here for that information. So here we go. To begin with, California’s climate is rivaled commercially by few in its fruit, grain, and vegetable growing capacity and beauty.
Yearly Taxpayers Foot $22 Million In Medical Costs for Farm Laborer Spine Injuries.
Back injuries are so prevalent with farm laborers one sector we discuss, grapes, has its work-related musculoskeletal disorder (“WMSD”) called a WRMD. But injuries to nerves, tendons, joints, cartilage, and vertebrae remain prevalent in the agricultural sector.
Picker and harvester work contribute significantly to back problems. And it can make pre-existing issues worse over extended periods.
A conservative estimate of the costs of medical and other bills of over 3,000 reported back injuries in the agricultural industry was based on a study involving more than 98,000 workers’ compensation claims from 45 states, including California.
The staggering total amounted to over $22 million in annual spinal cord injury charges to taxpayers. Even with new and automated technologies replacing expensive laborers swinging a flail, sickle, or winnower, workers and machine attendants will always be needed.
Why? Because someone still needs to clear jams and obstructions during the machine’s use. And mechanics and helpers be required for regular and emergency repairs.
Many of these machines have chopping, razor-sharp blades, and other threats. It is noteworthy that during these periods, a machine can suck or pull a worker in by catching a pant leg or shirt sleeve. When this happens, the probability of someone getting killed is highly high.
Most of all, someone is always at risk, no matter how many mitigating factors the agricultural and industrial complex takes.
As most visitors to the Golden State have observed, many pristine areas exist for growing and harvesting cash crop vegetables and plants besides marijuana. Also, with at least 270 days between its comparably light frost season, even the most vulnerable above-ground agriculture can survive to harvest.
So unlike the Red River Valley, freezing crops are almost non-existent in California farming. But in light of the tremendous costs involved with manual and even skilled labor, the race to replace farmhands with automated machines is on.
And the technology could potentially reduce agricultural injuries and jobs in one fell swoop. But for now, machines are a cause for concern, as the injuries they cause are often fatal.
Food Jobs = Accidents.
We recently discussed driver distraction and fast food accidents here and obesity and junk food here. But when you think about it, eateries are a link in the chain of agriculture that requires human laborers. Few can imagine an In-N-Out Burger without fresh or grilled onions. And when we choose fine dining, we often expect wine made from California’s best grapes and sugar refined from the most excellent sugar beets.
So it makes sense that a quarter or more jobs in the U.S. are connected in some way to the food and agriculture sectors! (Source).
As noted above, California has few ordinary growers, with its tenant and factory production monopolies over state agricultural production. From marketing, sales, and transportation, huge conglomerates and factory interests created the so-called “Sugar Trust.” And this is a nationwide phenomenon. (Source).
Labor Terminator – Rise of the Agricultural Machines!
Was the Terminator movie series right about the rise of machines? Possibly so. All types of human-controlled devices help people do things faster and sometimes better than humans.
Some machines make coffee, others shred paper, and others help farmers get food out of the ground without employing hundreds of laborers. Modernly, human-operated machines exist to support gathering a ripe crop from the field and getting it to market.
- Enter the Mechanical Harvesting Combine.
At the backbone of the reaping process is, of course, the mechanical harvesting combines in its many forms, shapes, and sizes. Most of all, efficiently run combines and harvesters remain the backbone of the reaping season for many types of mature crops.
Many of California’s fruit, vegetable, grain farms, and vineyards rely in some way on machine harvesters. Also called combines or combine harvesters, these particular machines help farmers and laborers efficiently reap some of California’s mainstay crops like sugar beets, onions, potatoes, and others discussed below.
Many types of human-operated, self-propelled, and farm truck-towed harvesting machines and accouterments exist. Below we will discuss the main harvesting and farm machines used to help California farmers and workers.
What Are The Various Types Of Harvesting Machines That Can Cause Personal Injuries?
Before we begin, readers need to understand that not the same machines can harvest all fields similarly. Other crops cannot be machine harvested at all. Why is that?
Besides the apparent nomenclature differences necessitated by engineering issues (e.g., some plants are high up, and others are buried in the earth), the number one answer is that machines can cause bruising to horticulture.
- Bruising is Why You Can’t Always Use Machines?
For example, the skin on fruits and vegetables provides a protective barrier, preserving the tillage yield until it reaches the consumer’s refrigerator or cupboard. Bruising fruits and vegetables leads to rapid rot and spoilage of entire vats.
So far, traditional machine harvesting has been most effective when harvesting crops with more rigid shells, such as grains, nuts, beets, sugar cane, etc.
- Advances in Genetic Engineering and Robotics Means More Types of Crops Can Be Machine Harvested.
True. With advances in science and technology, machine harvesting of traditionally hand-picked crops has exploded in recent years. Now, seeders and breeders can genetically modify the hardness and thickness of vegetables and fruits to make machine reaping more feasible.
Also, the tools are becoming softer on the items they pick, strip, and sort.
Robots are becoming more and more specialized for the types of crops and more ginger methods of stripping the valuable materials from the shrubs. Because of how individual plants grow, harvesting machines have adapted to their particular evolving circumstances.
For example, some species of beets and carrots are softer variants of underground roots. Other species have more complex skins and can withstand gathering blades, rollers, and shakers, stripping, and cleaning without bruising.
Like potatoes, combines for gathering roots and bulbs are adapted with low-to-the-ground vacuums and intake tillers. Comparing these units to those used for corn and wheat, you can see the size and height of the machines are different. And this is because these are above-ground plants, bushes, and trees reaped differently.
Below is a list of the types of harvesters used in much of California’s agricultural harvesting process. Also discussed are the various types of personal injuries attendant with these machines. The first class of devices we discuss is “Harvesters.” These harvesting contraptions remain more familiar for specific kinds of California agriculture.
The following types of machines are ancillary harvesters. Most of all, these are used to support harvesting crops and readying them for markets.
These machines are:
- Buckrake—for silage making
- Grain cart (with built-in Grain Auger)
- Conveyor belt
- Farm truck
- Grain dryer.
The main idea behind all harvesting machines is to tenderly remove the plants from the soil while separating the valuable fruits, grains, or vegetables from the other organic parts of the plant. The ancillary machines help move the yield to the various departure points.
The more dangerous mechanisms are discussed below, but each machine comes with risks of bodily harm during use or maintenance.
- Big Rigs and Trains.
Besides farm trucks, many other links in the chain of agricultural commerce exist. A yard truck is the industry name for a farm truck that pulls heavy trailers and looks like a diesel tractor. California Vehicle Code Section 4751d, 38010, and 38012 define yard trucks as yard goats, trailer spotters, terminal tractors, or jockeys that are purpose-built to haul trailers within or about freight operation yards, including docking bays at the Port of Long Beach, for example.
They aim to move merchandise or goods to the storage or loading bay area. Big rigs, prime movers, and other Jake Braking semis transport refined, distilled, or natural products to various loading docks at wholesalers, retail grocers, train and sea docks. Smaller trucks and delivery vehicles continue deliveries to other merchants, trading locally and far away.
Types of Combine Harvested Foods And Personal Bodily Injuries.
To recap, each combination is manufactured based on the type of crop. Better technologies and growing methods are moving towards one kind of machine with bolt-on or retrofit capabilities.
Farmers and related workers are most at risk for repetitive movement spine injuries, whereas farming machines place workers at risk for instantaneous, catastrophic injuries.
So let’s look at our first example of agricultural accidents and injuries using the California dry bean harvest model. Dry bean harvesting machines are first on our list of potentially dangerous devices for a farm worker or related tradesman.
California – Dry Bean Tillage And Mechanical Harvesters
Everyone loves tacos and beans in sunny California. But many ethnic beans exist besides Mexican or Cuban-style beans.
There are entire medleys of beans.
Mainly there are two types of beans:
- Green Beans.
- Dry Beans.
Asians desire green beans like Edamame and dry beans like Adzuki. Southern Americans seem to want dry bean varieties like Pinto Beans. And Central Americans like El Savadoreans favor smooth and silky red beans with their meals.
Green beans and dry beans are not the same regarding harvesting machines. Green beans, spinach, and corn use similar types of harvesters. So scroll down to corn to learn about those softer touch machine injuries involving combines.
The United States is the number one producer of dry beans. Yearly, U.S. farmers plant around 1.5 to 1.7 million acres of edible dry beans. (Source).
And this is why dry bean harvesting machines are at the top of the list. By the sheer volume of the harvest, statistically, the chances are more significant for a machine injury than a less-grown commodity.
Which Of The U.S. States Top the List in Dry Beach Production?
As seen below, California ranks number seven in dry bean production. So although it is not the top crop in the Golden State, we produce our fair share of dry beans. And thousands of workers are involved in the seeding and harvesting process annually.
1. | North Dakota | 32% |
2. | Michigan | 17% |
3. | Nebraska | 11% |
4. | Minnesota | 9% |
5. | Idaho | 8% |
6. | Colorado | 5% |
7. | California | 5% |
8. | Washington | 4% |
Per Capita, What Dry Beans Are Most Consumed In North America?
- Pinto beans
- Navy beans
- Great Northern beans
- Red kidney beans
- Black beans
California and dry beans go hand in hand. Pinto beans have become popular among North Americans with its large Mexican-American population. And this remains especially evident with consumers in Los Angeles and other high Latino populations.
Here is a map showing U.S. dry beans produced by variety. And plenty of International Food stores around Los Angeles sell all types of dried, bottled, and canned beans. Again, everyone in the chain of commerce is a potential personal injury victim.
What Are Some Dangers Associated With Dry Bean Harvesting?
Dry bean harvesters are a type of mechanical thresher or bean combine. The idea is that a “pickup” that looks like a giant electrical shaver mows the beans into a shaker and beaters. (See example).
These inner chambers vibrate the beans away from other organic materials like soil and pebbles. So as most combine, it pulls plant material in and shoots separated materials. But it is not a chopping machine like some others discussed below.
The gadget will generally be manufactured with a pickup, multiple beaters, and shakers. Other parts include fan systems and conveyor belts with elevators.
Like the Gold Rush TV series, conveyor belts will carry the suitable material to a storage bin and possibly a spreader at the rear that ejects other materials.
For years, The Bidwell Bean Thresher Company was the only widely available manufacturer of bean harvesters. Modernly there are many, all with different features and prices. Lubricating, maintenance, and cleaning out the combine are usually the times that workers get hurt or killed.
Here is an example of an owner’s manual for a popular dry bean combine. As you can see, in addition to the dangers of being sucked into the pickup, the operator’s manual states that there is an exposed, “rotating driveline.”
Also, there are overhead bin dangers, flying objects, projectile warnings, and high-pressure oil leaks to worry about. And on page 12, it says don’t work on the belts or equipment while the machine is running.
The risk of eye injury is always present in any machine with rapidly rotating teeth or pistons. And this remains true even when not repairing the machines.
So the manufacturer recommends that workers consistently wear eye protection. And there is still the risk of being crushed or run over. Last, many safety protocols for clearing blockages and safe operation of the machine are listed.
Knowing How Dry Bean Harvesters Work Helps Explain the Mechanisms of Injury
First, these machines are crucial in back injury avoidance for workers. Beans grow low to the ground. Workers are constantly bending over at the waist to pull and pick.
Because the crop is low to the field’s floor, the harvester contraption has its pickup low to the ground. Its function is to lift the beans and rapidly split waste products into windrows using rakes and pullers. Once elevated higher into the machine, the central conveyor belt feeds the material into the first beater.
After a series of blunt, rotating metal teeth, thresh the beans from their pods at high revolution to thresh the product and break apart the clumped-up beans. But like gold trammels, there is usually a process depending upon the type of machine that leads to different beaters and shakers.
All this powerful, moving equipment is at risk of malfunction. If the machine throws off a loose blade or something explodes, the people nearby are at risk for concussion and fallout.
- Maintenance and Clearing Blockages and Personal Injury
All of these fast-moving, distinct parts can become jammed or seized during the reaping process. When a jam occurs, other parts of the machine, like rotating rods, will be straining to work the rest of the unit.
Pressure can build, and something is going to break or fragment. Often, only excellent automatic failsafe devices can prevent things from getting out of hand.
Typically, workers on foot will follow along the field in front of the vehicle. Their job is to throw boulders and other obstructions in the row the path of the rapidly moving Combine.
These workers must ensure the machine’s intake or conveyors don’t get jammed up or stuck. So these workers, often day laborers, briskly clear debris and ensure no good beans are left behind.
But no matter how clear the tilled path seems, jams and breakdowns happen during harvest season.
So laborers are essential, and many don’t have the proper training to deal with a dry bean combine harvester.
What Are Some Common Injuries to Dry Bean Harvest Workers and Why?
We often hear about feet being injured or lobbed off by combine augers. Most of the time, the employer is trying to keep up a fast pace.
So if a problem exists in the feeding mechanism, a field hand will walk next to the pickup and clear jams rather than turn off the machine. But I am doing so risks clothing, jewelry, and body parts being grabbed and sucked into the belts and feeds.
Besides this, imagine a broken belt or metal piece flying at you at high speed because that is a real possibility with all these fast-moving metal parts.
But the number one way people get injured is when they are trying to clear out obstructions for the machine’s intake. Feet, fingers, and even heads can get crushed and amputated instantly. Of course, other injuries occur, like diesel fume poisoning, toxic weed killer poisoning, and various spinal cord personal injuries from repetitive bending and kneeling.
Most of all, the combine harvester is the number one death threat to workers. An experienced personal injury attorney who understands the limitations of compensation in workers’ compensation cases will be indispensable to an injured worker or non-employee bystander.
Only they can discover the potentially liable parties and unravel all the defenses and roadblocks to making a plaintiff whole.
California and Sugar Beets – Combination Harvester Personal Injuries
As the name suggests, sugar beets are related to table beets (Grandma’s Borscht comes to mind) but are consumed rarely. Instead, they remain the primary source of table sugar and as fossil fuel substitutes.
Important: California remains the nation’s largest supplier of sugar beets. California is now the second-highest sugar-beet-producing state. It yields precedence only to Colorado, which has long held the lead, with an annual sugar beet harvest of about 200,000 acres, or nearly twice that of California.
However, California is a much better second in tons produced, with 1,939,000 tons in 1936 compared to Colorado’s 2,227,000 tons. Other important sugar-beet states are Ohio, Michigan, Nebraska, Montana, Idaho, Wyoming, and Utah.
California and Table Beets.
sugarbeetes of San Bernardino and San Benito, with their warm, desert-like climates, grow more than half of the state’s table beet inventories annually.
In Imperial, for the past many years, combines have been a mainstay of the agricultural industry. Agriculture relies on these vehicles to enhance production and ensure that the harvests are adequately maintained.
Before introducing the harvester, three components made up harvesting grains: reaping, threshing, and finally, winnowing.
NOTEWORTHY: Sugarbeet Harvesting in California Sugar beets account for 55% of U.S. sugar production, where 5,500,000 tons oSugarbeetre consumed annually. Since 1870, 11 sugar factories have been constructed and profitably operated throughout California.
Since the passage of NAFTA, sugar exports in California have been hurt after being turned over to competitors in other countries.
And the last sugar beet factory in northern California closed in 2008, ending more than 140 years of beet production and thousands of jobs in those agricultural regions. Only one operating plant remains in the state (in the Imperial Valley).
California’s temperate zones and proper soil and production zones have proven vital to the Sugar Beet markets. Our topography and excellent climate, drainage, and seepage make certain areas, such as the Imperial Valley, great places to grow beets.
Water supply has always been a problem in California, which is another reason this deep-rooted vegetable is grown in the wetter areas of the state.
Also, it is not as hard on the soil as other crops. However, soil depletion can occur over time, like any plant grown continuously and not fallowed.
So many farms will maintain multi-use combines because they will rotate crops like peas, green beans, alfalfa, carrots, potatoes, lettuce, and tomatoes.
Beets – A Major California Crop
Sugar beets are genuinely a local vegetable, primarily due to their size and weight. Transportation of this bulky commodity is costly. Because of this, sugar beets rarely get shipped further than a thousand miles from their farms.
But the products distilled or derived from beets are quickly dispatched and sold worldwide. Even with the latest automation and safety advances, the labor involved in harvesting, packing, and shipping is still remarkable.
Remarkably, like corn, sugar beets are a tremendous fossil-fuel substitute, and they can make sugar. Some sugar beets get added to fuel ethanol production. Technically, converting pure sugar to ethanol is a straightforward process requiring yeast fermentation.
Contrast this with producing ethanol from starch, such as Sugar Beets. Beets are not a simple sugar but a complex carbohydrate, similar to corn or potatoes. So starch-based plants must be converted into simple sugars before they can become biofuels. To do so, enzymes convert the plant starch into sugars first.
As you can see, California’s carbon fuel restrictions make beets a valuable energy source for our state. But all beets are deeply rooted in the soil.
And manually ripping them from the earth is very time-consuming, physically strenuous, and likely to cause repetitive use back injuries, among others. Combine harvesters significantly reduce these problems, making harvesting more efficient and economical.
Sugar beet has evolved through time from a labor-intensive agricultural crop with a static yield to a highly mechanized one with steadily improving work. But they also bring risks of injuries and death on an enormous scale.
What Are Some Examples and Causes of Commercial Injuries Associated With Beet Harvesting Generally?
- Cancer. We have seen it in the news. Herbicides and weedkillers cause cancer. Combines kick up the soil as they dig it up. All this occurs as workers clear the machine’s path and remove jams. And weeds are a massive challenge for beet farmers in general. Weeds can kill the entire crop, and if not halted within the first eight weeks of sewing the fields, the harvest could be nil. (Source).
- Amputation, Dismemberment, Degloving, Blindness, Crush Injuries, and Death. Sugar beets are harvested with two primary pieces of equipment. The defoliator removes the green leaves and slices a slab from the top of the sugar beetroot. Imagine an arm or leg getting rung through a slicing device. This removed slab is the growing point of the sugar beet. It contains high impurities, impeding the factories’ ability to extract the sugar from the remainder of the harvested root. And it’s a worker’s job to keep this part of the machine precise, often while it’s running. The sugar beetroot is harvested with a pinch wheel harvester, which pinches the heart and lifts it from the soil. Getting caught in one of these wheel harvesters can mean certain death and injury. The sugar beet harvester also separates some dirt and conveys the sugar beet into a farm truck to be transported to a nearby receiving station. A body part sent into the machine will likely be incinerated, so it cannot be reattached.
In addition to the above, we have included some examples of Sugar Beet Harvesting Accidents and Associated Injuries in the News. Not all farm accidents are from combines. But take a look and see the risks associated with the harvest.
Worker Dies in Accident At Beet Co-Op.
Based on news reports, Decedent Erv Knutson, a 60-year-old male employee crane operator of 37 years, died at a Sugar Beet Cooperative when he was struck by a payloader outside a pallet loading area.
As part of the harvesting process, visibility obscuring steam vapors had developed due to condensation in the cold Minnesota weather. Of particular interest, a non-employee third-party contractor was the owner and operator of the offending payloader. Source).
As you can see, this fact pattern screams workplace-related health and safety problems. Steam decreased visibility, and another person independently operated a dangerous machine.
In California, the family may have had a shot at suing the employer and the third party for wrongful death. It takes a lawyer to make heads or toes of it all.
Sugar Beet Refining Plant Accident Falling/Crushing Death.
Again, it’s not always the harvesting machine that causes the injury. The entire harvesting process comes with risks, including the unloading docks.
For example, a twenty-eight-year-old beet plant worker, Anfesa Galaktionoff, died after falling into a piece of conveyor equipment meant to carry sugar beets into the refining factory. So Galaktionoff was crushed to death. (Source).
Accident: 202615324 – Employee Fractures Ankle Unclogging Beet Harvester
Below is a recent example of a Combine harvester injury reported by OSHA.
Accident: 202615324 — Report ID: 1054112 — Event Date: 09/26/2013
|
|||||||
Inspection | Open Date | SIC | Establishment Name | ||||
---|---|---|---|---|---|---|---|
317338382 | 09/27/2013 | 0191 | Thomas A Duyck & Vickie A Duyck | ||||
|
In the above example, you can get an idea of the mechanism of injury. As noted earlier, the Harvester became clogged with debris. So Employee #1 kept the tractor idle and went to clear the way.
The open slat conveyor and a solid steel roller grabbed and trapped the worker. No indication exists whether clothing or some other article like a shoelace began the pulling process.
And had it not been for the co-worker stopping the machine, Employee #1 could have been rapidly killed. Either way, there will be permanent mental and physical complications for years.
Wrongful Death Case – Rodriguez versus Osterkamp Farms
On May 19, 2015, at 3:30 a.m., decedent and one of the defendant’s beet harvester machine operators were near their respective autos. The two of them perhaps were at the rear of the beet harvester machine either talking or attempting to make mud clear from the harvester. At this point, the machine operator left the rear of the beet harvester, entered the cab of his tractor. So as decedent stood near the machine, the other man engaged the power. He did so even though he knew or should have known Rodriguez had been cleaning mud from the machine. So the operator negligently failed to check for a human in the area. So the harvester ran for 30-60 seconds. At this point, the operator walked back to the rear of the equipment. He then noticed the pieces of decedent’s mangled, dead body inside the harvester. (Source).
Like other crops, trucks often haul sugar beets to receiving stations. There they get weighed and offloaded onto sugar beet pilers. Another function of pliers is to remove more soil from the sugar beets, as they get stored in 18 feet tall, 1500 feet long “piles.” After beet samples are analyzed for their sugar content, tare, and overall purity, rehaul trucks are loaded with the approved sugar beets.
Truckers, such as the above decedent, are involved in delivering the sugar beets for final factory processing. Then, it is time to begin the process all over again. (Source).
Ehline has vast experience in all types of farm accidents, such as those above. Our firm helps workers in various farm accidents, from seeding to harvest. However, there are many more crops with their attendant risks to workers in the production chain. So keep on reading.
Personal Injury And California Carrots.
California’s carrot growers account for approximately 85% of fresh market production. So much so that the City of Holtville styles itself as the world’s Carrot Capital. This city even has an annual carrot celebration called the Holtville Carrot Festival.
And rightly so. After all, Daucus Carota grows year-round in many parts of California. Unlike beets and dry beans, carrots are shipped out of the state year-round. But California’s larger shipments take place from December through August. (Source).
California’s main production areas for carrots are where many labor accidents occur as follows:
- San Joaquin & Cuyama Valleys of Kern County & Santa Barbara County.
- Southern desert of Imperial County & Riverside County.
- The high desert of Los Angeles County.
- The central coast of Monterey County.
Consumer demand for uniform roots of deep orange and other colors, such as those sold in bunches at Whole Foods or Vons Pavillions, has led to the development of highly efficient Imperator-type hybrids.
Varieties for sold for the cut and peel market include:
- Sugarsnax.
- Top cut.
- Primecut.
- Trinity.
- Imperial Cut.
- Tastypeel.
But there are also Cello varieties under the brand names:
- Apache.
- Navajo.
- Maverick.
- Choctaw.
As you can see, catchy native American names are all part of the marketing game.
More About the Dangers of the Carrot Harvester Machine.
First of all, there are many types of carrot harvesting machines. For example, there is a top lift and a share lift machine. Simon typically manufactures these. These two kinds of harvesters collect carrots from the ground differently.
But all in all, a Carrot Harvester is used for harvesting carrots. Some carrot combines may be tractor-mounted, while others may be trailed behind a tractor. Still, other combines are self-propelled.
Commercial machines typically harvest between one and six rows of carrots at once. Like the other machines already discussed, workers help operate, maintain, and clear obstructions from the fields.
And when they do, sometimes people get seriously hurt or killed.
- Top lifting harvester injuries.
Top lifters present risks for pulling workers into their rubber belts as they grab the carrot’s green tops. Workers walking alongside are also at risk for foot and leg amputations and lacerations.
The following potential injury occurs when the carrots, with intact tops, are pulled into the machine, and the tops are cut off on their path to a waste chute out the rear. Imagine a hand or arm being lobbed off and spit out the tail into the field. These are real concerns for most laborers.
- Share lifting harvester injuries.
A share lifter uses a share to get the carrots out of the ground from underneath. The machine must be preceded by a topper with cutting blades that chop the green tops off the ripened carrot plants.
After, the carrots are carried on conveyors designed to sift away as much soil as possible. But the cutting blades have been known to come loose or get jammed.
Also, workers are hit by flying objects and debris when these things occur. Also, even after harvest, other injury risks are attendant with the cleaning and delivery process. The carrots are collected in a storage tank on the machine or towed trailers pulled in tandem.
Using a process called weeding, laborers have to clear away the freshly cut tops off of the machine, which presents a great chance of injury or death to the worker. (Source). Like other agriculture workers in every stage of the process remain at risk for injury and death.
Combine Grain Harvesters and Personal Injury.
The combine harvesters available today can combine all three steps into one smooth process. Consequently, harvesting grains is now more straightforward and efficient and helps stimulate the mass production of various grains.
Using a combine or harvester on a plantation leaves behind waste straw or the remaining dried leaves and stems on the field. The modern grain combines harvester, or fuse, can harvest various grain crops.
Like other harvesters, the name comes from its ability to perform multiple steps of harvesting operations as follows:
- Reaping.
- Threshing
- I am winnowing—into a single process.
Among the grain crops harvested with a grain combine are:
- Wheat.
- Oats.
- Rye.
- Barley.
- Corn and maize are discussed below.
- Sorghum.
- Soybeans.
- Flax (linseed).
- Sunflowers.
- Canola.
Last but not least, grains are a significant source of animal feed, like straw. The scattered straw on the field comprises the stems and any remaining leaves of the crop with limited nutrients left in it: the straw is then either chopped, spread on the ground and plowed back in or baled for bedding and limited feed for livestock.
Often, these chopping machines can rip an arm off or operate like a bear trap, leading to a slow, painful death.
Combine harvesters are one of the most economically critical labor-saving inventions, significantly reducing the fraction of the population engaged in agriculture.
The leftover waste straw contains limited nutrients. It is usually chopped and scattered across the farming field. Sometimes the remaining straws are baled and fed to livestock or utilized as bedding.
The grains that are most commonly machine-harvested are:
- Barley.
- Flax.
- Oats.
- Rye.
- Soybean.
- Wheat.
To recap, combined harvesters have undergone tremendous development with the introduction of safety and technological advancements in machinery. Also, as part of a team effort, ground crews and operators have learned to optimize the machine’s harvesting speed and systems to increase yield.
And, of course, in California farm country, more and more combine harvesters travel along highway shoulders and roadways.
Sadly, in addition to grain harvesting injuries to workers, people get into terrible combined involved traffic wrecks. Think about it, a slow-moving vehicle, even with a sign to alert other drivers, is no assurance of a safe ride.
Besides, this is a fast-paced job and every second counts. Because of this, farmers may enter roads with dirty windshields, drive at unsafe speeds, and fail to signal or use proper lighting. Recently in the news, we have seen a spike in railroad crossing accidents with combines.
- Grain Storage Silos Personal Injury.
Many terrible grain deaths and accidents center around the storage silos and bins. First of all, cleanliness is safety. A clean grain storage bin area helps prevent many types of grain accidents.
Next, the moisture content in the grains before storage is vital to worker safety. For example, imagine a farmer trying to loosen up water-cemented grain with a pick-axe or rake as he tries to loosen the hard grains and empty his bin.
Even a leaky bin can allow the grain to become wet and heavy. As the worker begins to loosen up the clumps, an avalanche of thousands of pounds can fall on the worker, crushing and killing him.
Negligent employers should have made inspections, but now it’s too late. Someone is dead. Grain bin safety means fewer funerals. So do your part to avoid future grief.
California Onion Harvests and Personal Injury.
California is the largest onion producer in the U.S. Also, California remains the only producing summer and spring harvests of eye-watering vegetables.
In 2015, the Golden State grew 31% of the nation’s total onion yield. Counties at risk for the most onion harvesting injuries are Fresno, Imperial, Kern, Siskiyou, and San Joaquin.
Also, a small enclave for onion-related injuries exists in the high deserts regions like L.A. County’s Antelope Valley and the Salinas Valley.
Injuries commonly happen when pickers snap the rolls to keep material flowing into the feeds and separators.
What Machines Used For Onion Harvests?
- Mowers: Mowers are especially hazardous to farm workers. Typically, sharp, rapidly rotating blades mow the tops of the onions off. However, knives have been known to fly off and kick up a lot of soil and dust. So, in addition to lacerations and cuts to the lower extremities, eye injuries remain common in mowing jobs.
- Windroller: This machine is designed to uproot the onions from the bottom up. Afterward, the onions run along a conveyor system designed to clean soil from the vegetables, depositing them into a single row collected by workers.
- Topair Combines: This machine picks up two rows of onions at a time and blasts them with air into a collection area where laborers hand-sort the vegetables. Next, workers will load the approved onions into an adjacent trailer or bin that gets towed to a packinghouse for shipment. (Source).
As noted above, onion harvesting still requires a lot of machines and human interaction, regardless of the type of harvesting methods.
Also, as with other combines, there are a lot of rapidly moving and sensitive parts. As such, machine and different spinal cord-related issues remain prevalent with onion workers.
Harvesting Onions at Night and the Risks to Workers?
Because onions remain at significant risk for sunburn most of the time, onions are harvested at night. Laborers typically begin the hand-harvest process in the late afternoon and work till midnight.
Next, the machine harvester takes over to do their part of the job, perhaps till around the following afternoon. The machines will still move, even if jammed or plugged in. But now, the stalks can bunch up all around the rolls.
And that blocks the stalks being harvested from being grabbed into the harvesting machine. And this is when farmers are in a hurry to get work done to try and clear the jams or clogs without shutting down the picker machine and tractor. When moving, the farmer may grab a stalk to pull it out.
But this may be enough to make the machine quickly jerk the worker into the contraption before he can even let go of the plant material.
Now, the worker’s arm is sucked into snapping rollers traveling approximately 12 feet per second. So that would give a worker pulling a branch two feet long less than half a second to let go before losing a limb. Often, the worker is startled and cannot react in time to prevent this type of accident.
TIP: Always turn off the machine when you stop. Disable the blades and pullers before clearing jams!
EXAMPLE: Man dies after being pulled into onion harvester
Authorities identify a man killed in an onion harvesting machine accident in rural Oregon. (Source).
And be careful, this could be you: On October 19, 2019, 42-year-old Theodore Frahm was killed in an onion harvesting machine accident.
Frahm and others were working on farm equipment used to harvest onions and at one point the equipment was turned on and pulled Frahm into the equipment, according to the news release. (Source).
As you can see, combined harvesters being turned on when a person is near the machine is a significant cause of farming deaths. Employers, manufacturers, and others may have all played a part in causing these mishaps.
So they are all potentially on the hook to pay you or the surviving family. That is why it is crucial to get legal advice before agreeing to anything or giving statements to investigators. And this is in addition to the other calamities discussed above related to harvesting machines.
Corn Harvest Injuries in the Golden State.
Corn is America’s number one cash crop, worth over $47.38 billion in 2008 alone. California ranks number two for corn production nationwide. And it grows and harvests 16% of all sweet corn in the U.S.
However, most of California’s corn is converted to hay, or animal feed, for dairy cows. Corn harvesters, like other combines, harvest corn based on its unique plant configuration.
The process starts by stripping the stalks protruding around one foot off the ground. Next, it shoots the stalks into a header and reaches the floor after the corn is stripped away. But the corn products continue their journey through the title to the intake conveyor belt.
Next, the conveyor belts send the kernels into a fan system, which divides up any still intact stalks from the corn ears.
The remaining stalks are then blown out of huge ducts into the field. And the corn ears are moved to another conveyor belt and dumped into a large moving bucket. A forager, hay, or chopper are all variations of this arm implement designed to turn forage plants into hay or animal feed.
Silage can be made from corn, hay, or grass chopped up into tiny pieces and pressed into bails or sillage bags.
But often, surpluses are placed in storage silos. And these bins are also called bunkers. Making sillage includes a fermentation process to convert it into livestock feed.
What are the Top Counties for a Sillage Harvester Injury?
- Imperial.
- Fresno.
- San Joaquin.
- Contra Costa.
- Riverside.
California corn for sillage production was valued at $182 million in 2010, up 48% from 2009. There are many laborers and workers involved in corn and sillage production. The National Agricultural Safety Database claims that almost any farmer, friend, neighbor, or family member knows of somebody hurt or killed in corn picker machine accidents.
Many corn-picking machine deaths happen due to faulty hydraulic cylinders.
Also, many industrial picker machines are more significant than those used for other crops like beets. These larger machines present blind spots to operators, placing field workers at risk of being crushed or run over.
In an agricultural area like Santa Paula, California, you may have seen these wider-than-normal combines pacing slowly along the highways with “Wide Load” signs and flashing emergency lights. This makes operating these machines particularly dangerous to other road users and motorists, especially motorcycle riders.
So it goes without saying that corn picker accidents have led to many injuries and deaths in the geographical areas they operate. Most of all, farms, feedlot, dairy, and silage contractors should train their employees in proper silage production safety. And they should have regular safety meetings. Getting people back safe to their families should be every boss’s goal.
Grape Harvester Personal Injuries.
California produces 90% of the grapes grown in the United States and 7.7 % worldwide. As a result, California is ranked number one in the nation’s production of wine, wine grapes, table grapes, and raisins.
Workers in the grape industry have long had various work-related Work-related musculoskeletal disorders (“WRMDs”). WRMDs are hard to classify under traditional disease classifications.
But we know that symptoms include constant pain, and loss of function and can result in total physical disability. Like CMP or Patella Femoral Pain Syndrome, their initial diagnosis is difficult since they are based on subjective pain symptoms. But substantial evidence exists that WRMDs are high among wine grape vineyard workers. Perhaps it’s from ergonomic risk factors associated with many repetitive agricultural jobs. (Source). For example, this type of work involves body vibration and routine overhead picking. Because of this, the neck remains in a chronic and repetitive flexion position during forceful, strenuous tasks.
For years, scientists and engineers have been looking for ways to cut out laborers and the associated costs of pensions, retirements, and medical care insurance. Also, harvesting machines, as discussed above, have often caused more harm to soft-skinned grapes than any good they did by yield increase. But as concerned, with genetic engineering and better machinery, WRMDs could soon be a thing of the past for grape harvesters.
Machine Harvesting of Grapes.
Picking grapes bay is a very labor-intensive and injury-prone affair. Recent advances have led to viable machine harvesting. Although it is more efficient in almost every way (can pick, crush, and chill in half an hour or less), compared to handpicking, which takes a gaggle of expensive laborers and at least four hours to achieve the same process.
- How Do Grape Harvester Machines Work?
Mechanical grape harvesters use bow-like rods to remove the berries from their host plant’s cluster.
The idea is to leave the rachis behind on the vine. Less efficient machines were used in the past. But the newest generation of grape harvesters is even better at de-stemming and sorting Material Other than Grapes, or “MOG.” So that cuts out the need for more laborers to de-stem and sort at the winery itself.
Example of Recent Grape Harvesting Machine Accident in the News.
As discussed on www.ehlinelaw.com, maintenance and on-the-spot fixes of these machines are when people get hurt most. For example, just recently, a field worker was killed after he tried to clear an obstruction from a grape harvester.
Leon Marcelo Lua, 49, was killed after he tried to unclog a grape harvester by reaching into a rotating shaft, according to the federal Labor Department and Napa County Sheriff’s Office.
The shaft caught his sweatshirt, pulling him into the machine and killing him. According to OSHA records, a colleague turned the engine off and tried to render aid to him, but his body went limp after a few seconds.
In the newsworthy example above, an article about Lua’s loose clothing became stuck in the machine’s rotating shaft. So here is one example of poor worker safety and training.
For whatever reason, decedent Lua was working on a moving machine designed to grab and pull things in! As the trend moves towards the mechanical harvesting of raisins, we expect to hear more stories of worker deaths.
Sure, the government can fine or penalize the farming conglomerates, but how does that pay the survivors? In the above case:
…..violations issued included one for failing to guard a revolving shaft, and another for failing to turn off an engine before trying to unclog, clean or otherwise service a piece of equipment, according to OSHA’s website. (See above source)
So the question is, what does Lua’s family do now? These are the questions we attempt to answer further down. But there is hope, even after the grief of wrongful death.
Over-the-row mechanical harvester for harvesting apples
Hand-harvesting, the U.S. apple crop, is labor-intensive. And now that apple cider, or ‘hard cider,’ is becoming popular, fermented apple juice has become a hot commodity in the U.S. liquor industry.
Of particular interest, we saw a 65% increase in production from 2008 to 2014. Because of this, cost-effective means of harvesting have led to experimentation with many machine configurations for apples.
Mechanical over-the-row ‘shake and catch’ harvesters are designed for smaller hand “Brown Snout” and “Malling” apple graft mixes. And these are grown on a low trellis.
Enter The Vacuum Harvester!
Farmers have sought an effective and efficient vacuum harvester for apples and oranges for years.
But it appears that DBR Conveyor Concepts has developed a two-part system that includes:
- A self-propelled Brownie Quad platform.
- And a vacuum harvesting unit.
Now, this crew-served machine can reduce the laborers to four pickers. Their primary mission is to man the hydraulic platform picking the tree apples as high as 13-14 feet.
The methodology is to place each apple into a foam-lined vacuum receiver tube. This tube rapidly carries the apple away at a fantastic speed of 12 feet per second. Once the apples approach the distributor wheel, foam-lined deceleration wheels slow the apple down, gingerly dropping it onto a distributor wheel into a bin without bruising the fruit.
What About the Pluk-O-Trak?
Munckhof’s Pluk-O-Trak harvester combines reconfigurable hydraulic platforms. It can be used for pruning, hand thinning, and even trellis maintenance.
Also, these machines come equipped with pulling conveyor belts to carry their apples to storage containers. Loose clothing and jewelry can catch on these fast-moving belts as the fruit picker places the apple onto a designated finger sending it to a rotating bin filler.
The fingers on the belts help avoid bruising of the apple’s skin on the way to the container. The machine’s builder asserts that “fruit quality is increased by 50% to 60% compared to conventional harvesting methods.”
Using a crew of six to eight people and no risk of falling from ladders, severe injury, and death risks are significantly mitigated. Also, the workers expend less physical energy and strain, which helps reduce fatigue, heatstroke, and heat exhaustion.
Other Ideas to Help Farmers Avoid Injury?
Researchers are perfecting ideas like:
- A shake and catch system that specifically targets the tree canopy and then catches the fruit directly beneath to reduce fall bruising and damage from scraping against or hitting branches or other fruit.
- A crop load estimation tool utilizing machine vision that computes the number and size of each piece of tree fruit to estimate crop size.
- I am using crewless aerial vehicles (“UAVs”) to scare off birds, rodents, and other threats to cherry, blueberry, and grape crops. (Source).
Over the Row Mechanical Harvester – Citrus Harvesters.
Like apples, over-the-row mechanical harvesting machines are also used for dwarf and young citrus trees. But these fruits are gathered using the same devices that reap blueberries and olives.
The future wave is the versatile citrus harvesting machines that can be adapted for different crops. But retrofitting will bring with it new injuries to workers. Some of these advances in the mechanization of citrus harvesting are published in IJABE. (Source).
Potatoes and Personal Injury.
Because of California’s fantastic climate, it remains the only state capable of harvesting potatoes year-round. Potato harvesters are machines used for harvesting potatoes.
Like Beet harvesters, they work by lifting the potatoes from the earth’s soil bed using a share. Soil and crop are transferred onto webs where the loose soil is sieved out.
The potatoes are moved towards the back of the harvester onto a separation unit and then (on operated machines) to a picking table where people pick out the stones, clods, and haulms (stems or stalks) by hand.
The potatoes then go onto a side elevator and into a trailer or a potato box. Like other machines, pesticide-filled soil gets kicked up, and eye injuries are common. Back injuries remain the mainstay of these field worker injuries.
Potato spinner injuries.
A potato spinner is attached to a tractor via its three-point linkage or hitch that pulls a flat piece of metal that runs horizontally to the ground. As it digs into the earth, potatoes are lifted by a large wheel with spokes called a reel.
All the while, tilling motion pushes clay and potatoes off to the side without bruising them. After, laborers will usually bend over and place them into bags or baskets and then move away from the field for packing and distribution.
Haulm topper injuries.
A haulm topper cuts potato haulms off before harvest. Like a flail mower, some potato farmers will mount a haulm topper in the front of their tractor and tow a potato harvester behind it. But some toppers are rear-mounted.
The machines have many blind spots and other potential grabbing risks inherent in harvesting machines.
Farm Accident: Potato Harvester Crushes Worker’s Leg
While performing maintenance on a potato harvester, a farmworker fell, and his leg was caught and then crushed. This slide show tells the story of this workplace accident. (Source). As can be seen, farm injuries are far more common than one might think.
Sugarcane Harvester Injuries.
“If you take the [Metro] Blue Line to Long Beach, from the train, you’ll see a lot of homes with sugar cane growing in the backyard.” (Source LA Times). But with our water crisis, California will have difficulty sustaining more than a few hundred acres of cane in a season. Sugarcane has been successfully grown in California’s Imperial Valley for decades.
The soil is relatively rich with deep alluvial clay loam and, with the availability of irrigation water due to the Imperial Valley’s priority allotment of water from the Colorado River basin, is well-suited for farming. The area is recognized as one of the most productive agricultural regions in the world.
Due to the dry climate, intense sunlight, and irrigation, Imperial Valley sugarcane can be planted and harvested year-round, unlike Florida, Louisiana, and Texas, where rain limits the harvesting season to six months. (Source).
A sugarcane harvester is a giant piece of farm equipment used to harvest agriculture and partially process sugarcane. The machine remains similar in function and design to the traditional combine harvester. So, it essentially comes with a storage vessel on a truck with an automatic extension.
From there, the machine cuts the stalks at the base, strips the leaves off, and chops the sugar cane into various segments stored in an onboard container or a separate tandem vehicle.
Also, any waste product is shot out of the field, where it is recycled as plant fertilizer.
- Types of Combines on the California Market:
For example, the sweet spot in harvesting potatoes and onions lies in digging them up and ripping their roots from the earth without injuring or tearing the vegetables’ skin.
The farmer’s choice of harvester plays a significant role in deciding this. The cost of fuel and maintenance is also part of the balancing factor. Some harvesting combines that may harm the vegetables less are so expensive that they could be a wash.
Some of the harvested items will be destroyed during harvesting. So the total operating costs will always play a role in the choice of machinery selection.
A regular gas motor will have higher running and maintenance costs, despite lower gasoline prices when compared to diesel fuel. As a result, the low-maintenance Cummins Diesel is among the most popular combined engines for vehicle manufacturers.
And like the big rigs that haul farm products, diesel engines, in general, are the preferred types of motors powering most combines in California.
IMPORTANT: Besides the risks attendant with harvester machines, workers face toxic exposure to diesel fumes while working in the fields.
The more popular combined manufacturers are as follows:
- Case IH.
- Challenger.
- Claas.
- Class Lexion.
- Ford.
- Gleaner.
- International.
- John Deere.
- Lexion.
- Massey-Fergusson.
- New Holland.
To recap, workers can be injured in many long and short-term ways. In the agricultural industry in the US, harvesters play a vital role in overall production. However, harvester accidents are a pervasive problem in every state. Harvester vehicles pose many dangers to the users and people close to this heavy machinery.
Also, harvester accidents are frequent, contrary to what many may believe. Such accidents are often the most disastrous, with severe injuries and even fatalities.
For this reason, individuals working near harvesters must exercise the utmost care to avoid being sucked inside and mangled or killed.
Safety Training is Key.
Farm work, including harvester combine deployment, means exposure to many large, dangerous moving machine parts. Most accidents occur because of a problem with one of these moving parts.
Because of this, workers must be adequately trained in safety. Staying safe and alive means attention to the minor details.
Some of the worst dangers involving harvester accidents are:
- Incorrect use of straw chopper or spreader equipment towed at the vehicle’s rear.
- Entanglement of workers with the grain tank leveling or discharge area.
- If a cutting system tugs, yanks, or pulls a worker into its mechanism.
- They were being sliced and cut up by the rotating reel, knife, or stripper rotor.
- The machine’s header unfastens itself from the transport trailer.
- The automatic sensor system hurts or traps the user.
- When a harvester collides with a person or thing.
Some More Safety Tips for Combine Users.
Some safety tips while using combines are as follows:
- Assess field losses regularly. In other words, ensure the machine is not damaging, losing, or destroying more than 1% of the yield during harvest.
- Drive at a safe speed for the conditions. Don’t run down your field workers. And don’t go so fast. You jam the intakes. Find the sweet spot for total separation efficiency.
- Never refuel a hot combine. Burn injuries from ignited fuel vapors happen fast in 100 degrees plus weather. Add a hot engine to this, and a vapor explosion is possible. Most combination fires occur during the refueling process.
- Maintain a proper fire extinguisher. And make sure it can be accessed from ground level so you don’t have to enter the cab of a burning vehicle to grab it.
- Undertake routine maintenance. Before starting your shift, make sure and grease the vehicle and check for safety issues.
- Pay attention to your surroundings while driving. Stay hydrated, get plenty of rest, and stay calm when operating the vehicle.
- Maintain a cushion of space from other machines and autos. Always remember that you are controlling a massive engine capable of killing people. Always be relaxed, and always know where you are. Exude confidence.
- Clear away soil, mud, and other debris like chaff left from the machine regularly. Make visual inspections of the rotating shafts, axle, other bearings, and conveyor belts. If something sounds wrong with the device, there could be plant material or another object trapped or wrapped around some of the internal areas of the device.
Don’t forget that California employers must create an IIPP or Injury & Illness Prevention Program. Your employer should pre-plan accidents so a system is in place to investigate illnesses and injuries. Your employer is also supposed to plan for near misses during the day.
Also, employers must investigate and document details of any farm accidents in writing. Typically, HR or someone most knowledgeable about the law handles these reports.
Drones and Evidence Gathering?
Autonomous systems and drones will be used increasingly in harvesting and planting crops. These will all be equipped with cameras and be crew-served. Machine jams will still have to be cleared; other issues will require human hands.
As your attorney, we will rapidly send out demands to preserve this evidence to prove whether a product defect or failure by the employer caused these injuries or deaths.
Farm and Combine Machine Accident Lawyers.
Ehline Law Firm Personal Injury Attorney has proudly provided you with the most up-to-date, cutting-edge information on your rights, duties, and obligations as an employee and an employer when a severe injury occurs on a farm.
Harvesting combines can kill you or help you. But there are other injuries and accidents besides those caused by combines during the entire food production chain.
Only an attorney can help you maximize the money you can get for yourself or your family in these complex and confusing cases. If you suffered a farming or harvesting machine accident, our personal injury lawyers are ready to help you with your employment or third-party lawsuit claims.
You may be entitled to compensation, so don’t sleep on your rights. We help suffering clients in Los Angeles, San Bernardino, Imperial County, Sacramento, and Southern California.
Schedule a Free Consultation With A Combine Accident Lawyer In Los Angeles Today!
We have been trustworthy advocates to thousands of clients over the past 15 years. Call us to learn more about your rights, duties, and obligations in a case like this before the statute of limitations expires. Get the compensation you deserve by calling (213) 596-9642.